Introduction
Diesel generators are essential power backup solutions that provide electricity during outages or in areas with unreliable grid power supply. In humid climates, where excessive moisture in the air can pose challenges for equipment operation and maintenance, it is crucial to understand how diesel generators can be effectively utilized. This comprehensive guide will explore the considerations, challenges, and best practices for operating diesel generators in humid climates.
Chapter 1: Understanding Diesel Generators
Diesel generators are a type of internal combustion engine that converts diesel fuel into mechanical energy to generate electricity. They are commonly used in various applications, including residential, commercial, industrial, and construction settings. https://www.lkpowerplant.com of a diesel generator include the engine, alternator, fuel system, cooling system, and control panel.
In humid climates, the ambient air moisture can affect the performance and lifespan of diesel generators. The high humidity levels can lead to condensation, corrosion, and moisture ingress, which may compromise the generator's efficiency and reliability. Proper maintenance and operational practices are crucial to ensure the optimal performance of diesel generators in humid environments.
Chapter 2: Challenges of Operating Diesel Generators in Humid Climates
Humid climates present unique challenges for operating diesel generators due to the increased moisture content in the air. Some of the common challenges faced by diesel generators in humid environments include:
1. Condensation: High humidity levels can lead to condensation inside the generator components, such as the engine, alternator, and electrical connections. Condensation can cause rust, corrosion, electrical shorts, and other issues that may affect the generator's performance.
2. Corrosion: The presence of moisture in the air can accelerate the corrosion of metal components in the generator, such as the fuel system, cooling system, and electrical connections. Corrosion can lead to leaks, blockages, and malfunctions that can result in downtime and costly repairs.
3. Air Filtration: Humid climates often have higher levels of airborne particles and contaminants, which can impact the air filtration system of the generator. Dust, dirt, and debris can clog the air filters, reducing airflow and causing overheating of the engine.
4. Cooling System Efficiency: High humidity levels can affect the cooling system of the generator, reducing its efficiency in dissipating heat generated during operation. Overheating can lead to engine damage and decreased performance of the generator.
Chapter 3: Best Practices for Operating Diesel Generators in Humid Climates
To overcome the challenges of operating diesel generators in humid climates, it is essential to implement best practices for maintenance, operation, and monitoring. By following these practices, generator owners can ensure the reliable performance and longevity of their equipment in high humidity environments. Some of the best practices include:
1. Regular Maintenance: Scheduled maintenance is crucial for diesel generators operating in humid climates. Regular inspections, cleaning, and servicing of components such as air filters, fuel filters, cooling system, and electrical connections can help prevent issues caused by moisture and humidity.
2. Moisture Control: Implementing moisture control measures can help mitigate the effects of high humidity on diesel generators. This includes using dehumidifiers in the generator room, ensuring proper ventilation, and sealing off openings to prevent moisture ingress.
3. Corrosion Protection: Applying corrosion-resistant coatings to metal components of the generator can help prevent rust and corrosion. Regular inspections for signs of corrosion and timely repairs or replacements can extend the lifespan of the generator.
4. Air Filtration: Regularly check and replace air filters to ensure optimal airflow and prevent the entry of contaminants into the generator. Installing high-quality air filters and maintaining a clean environment around the generator can improve its performance and efficiency.
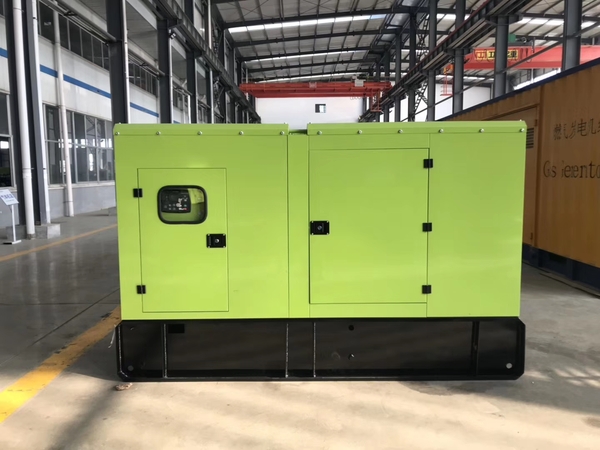
5. Cooling System Maintenance: Inspect and clean the cooling system components, such as radiators, fans, and hoses, to ensure proper heat dissipation. Monitoring the coolant levels and ensuring the cooling system is functioning effectively can prevent overheating and engine damage.
Chapter 4: Fuel Management in Humid Climates
Fuel management is a critical aspect of operating diesel generators in humid climates. High humidity levels can lead to fuel contamination, microbial growth, and degradation, which can impact the efficiency and reliability of the generator. Proper fuel management practices can help address these issues and ensure the uninterrupted operation of the generator. Some fuel management best practices include:
1. Fuel Quality Control: Use high-quality diesel fuel that meets the manufacturer's specifications for the generator. Regularly test the fuel for water content, particulate matter, and microbial growth to ensure it is clean and free from contaminants.
2. Fuel Storage: Store diesel fuel in clean, dry, and well-ventilated tanks to prevent moisture ingress and contamination. Use fuel additives and stabilizers to extend the shelf life of the fuel and inhibit microbial growth in humid conditions.
3. Fuel Filtration: Install fuel filtration systems with water separators and particulate filters to remove contaminants from the fuel before it reaches the engine. Regularly inspect and replace fuel filters to maintain the cleanliness of the fuel system.
4. Fuel Sampling and Testing: Periodically sample and test the fuel for water content, microbial growth, and degradation. Develop a fuel testing schedule and follow the manufacturer's recommendations for fuel quality control to prevent issues related to fuel contamination.
Chapter 5: Monitoring and Remote Management
Monitoring and remote management systems can enhance the operation and maintenance of diesel generators in humid climates. These systems allow generator owners to track performance metrics, diagnose issues, and implement preventive maintenance measures from a remote location. Some key benefits of monitoring and remote management systems include:
1. Real-time Performance Monitoring: Monitor the generator's key performance parameters, such as fuel consumption, temperature, and load, in real time to identify anomalies and potential issues before they escalate.
2. Remote Diagnostics: Diagnose and troubleshoot generator issues remotely using monitoring systems that provide alerts and notifications for maintenance requirements or malfunctions. Remote diagnostics can reduce downtime and improve the efficiency of maintenance activities.
3. Predictive Maintenance: Implement predictive maintenance strategies based on data collected from monitoring systems to anticipate and address potential failures before they occur. Predictive maintenance can extend the lifespan of the generator and reduce maintenance costs.
4. Energy Management: Integrate the generator with energy management systems to optimize its operation based on power demand, grid availability, and energy efficiency goals. Energy management systems can help reduce fuel consumption and operating costs while ensuring reliable power supply.
Conclusion
Operating diesel generators in humid climates requires careful consideration of the unique challenges posed by high moisture levels in the air. By implementing best practices for maintenance, fuel management, and monitoring, generator owners can ensure the reliable performance and longevity of their equipment in humid environments. Proper maintenance, moisture control, corrosion protection, fuel quality control, and monitoring systems are essential components of a comprehensive strategy for operating diesel generators in humid climates. By following these guidelines, generator owners can optimize the performance and efficiency of their equipment and minimize the impact of humidity on generator operation.